- solutions
- industries
- about us
- resources
Resources - Blog - Business
July 22nd, 2024
Sustainability
The Role of Silicon in Decarbonisation
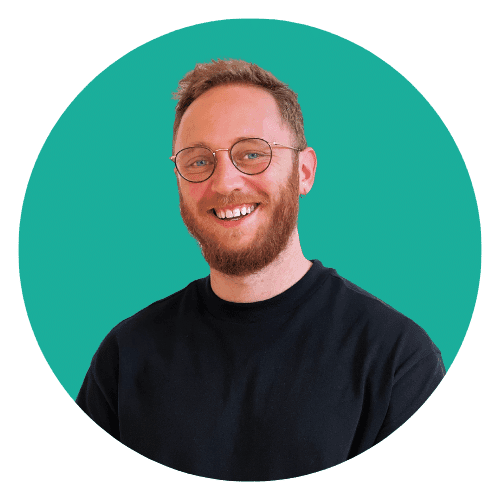
Jordan Lindsay
Silicon plays a pivotal role in decarbonisation efforts, particularly in photovoltaics, semiconductors, and lithium-ion batteries. In photovoltaics, silicon is the primary material in solar cells, converting sunlight into electricity efficiently and sustainably. As a key component in semiconductors, silicon drives advancements in energy-efficient electronics, reducing overall energy consumption. Additionally, silicon is increasingly being explored for use in battery anodes, promising higher energy densities and longer lifespans for electric vehicle and grid storage batteries. Together, these applications highlight silicon's critical contribution to reducing carbon emissions and fostering a sustainable energy future.
At a glance
- Silicon is important to society because of its utility in multiple important technologies that are ultimately reducing our reliance on fossil fuels - solar panels, batteries and semiconductors.
- Silicon adds value to businesses through diversifying and enhancing technology solutions for various applications, for example, forming high energy density anode solutions, cutting-edge solar energy or intricate electronics.
- The most important impact category linked to silicon is climate change potential, as the main aim of the above solutions is to decarbonise society; with high energy demand for high purity silicon products, it is essential that this key material is processed using sustainable energy or manufacturers face the risk of emitting equivalent emissions as old technology indirectly!
Silicon use in modern society
Silicon, the second most abundant element in the Earth's crust, is primarily obtained from silica (SiO₂, also known as quartz), found in sand, quartz, and various minerals. The leading producers of silicon are China, Russia, Norway, and the United States. China dominates global production, accounting for more than half of the world's supply, primarily through the mining of quartz and its reduction in electric arc furnaces.
In downstream applications, silicon's journey begins with its extraction and purification, and ends in the highly specialised manufacturing of three key technologies:
- High-purity silicon is essential for the semiconductor industry, where it is transformed into wafers for microchips that power a multitude of electronic devices. These semiconductors are crucial for energy-efficient technologies, contributing to global decarbonization efforts.
- Photovoltaic (PV) applications require high-purity silicon as well. China, the leading producer of solar-grade silicon, has extensive manufacturing facilities for silicon wafers used in solar panels. These panels convert sunlight into electricity, playing a vital role in renewable energy production and reducing reliance on fossil fuels.
- For battery anodes, especially in lithium-ion batteries, research is ongoing to enhance performance using silicon. Although not yet as widespread as graphite, silicon anodes are promising due to their higher energy density, which could significantly extend the range of electric vehicles and improve grid energy storage solutions.
Thus, the global silicon supply chain, driven by key producing countries, underpins crucial technologies in semiconductors, photovoltaics, and advanced batteries, all pivotal in the transition to a low-carbon economy.
Beyond its use in PVs, semiconductors, and anodes, silicon plays a crucial role in various other industries. It is fundamental in crafting construction materials like concrete and glass, and is used to create silicones for sealants, adhesives, and medical devices. Silicon compounds are essential in ceramics and refractories for high-temperature industrial processes, and silicon carbide serves as a key abrasive material. Additionally, silicon is vital in optical applications, such as optical fibres for telecommunications and lenses. These diverse uses highlight silicon's versatility and importance to humanity.
Silicon processing
There are different requirements for silicon processing and refining for photovoltaics, semiconductors, and anodes, primarily due to the varying purity levels needed for each application (Ceccaroli et al., 2016).
Silicon used in PVs must have a purity of around 99.9999% (6N purity), which is sufficient for efficient solar cell performance. Silicon for PV applications is produced via the Siemens process, where metallurgical-grade silicon is purified into polysilicon. This involves energy-intensive steps including chemical vapour deposition, where trichlorosilane (SiHCl₃) is decomposed into high-purity silicon.
Silicon used in semiconductors must be of extremely high purity silicon - usually 99.9999999% (9N purity) or higher. The presence of any impurities can significantly affect the performance of semiconductor devices. Silicon for semiconductor applications undergoes additional refining steps beyond those used for PV silicon. The Czochralski (CZ) or float-zone (FZ) processes are commonly used to grow single-crystal silicon ingots, which are then sliced into wafers. The CZ process involves melting high-purity polysilicon and growing a single crystal from the melt, while the FZ process involves melting and recrystallising a polycrystalline silicon rod to produce ultra-pure single crystals.
Silicon used in lithium-ion cell anodes does not require as high a purity level as that for photovoltaics or semiconductors. Typically, metallurgical-grade silicon, with a purity of around 98-99%, is used, which then undergoes fewer refining steps. The manufacturing focus is more on particle size and surface modification, which both enhance battery performance rather than achieving extremely high purity.
ESG challenges in the silicon supply chain
The silicon supply chain, critical for technologies in semiconductors, photovoltaics, and battery anodes, faces significant environmental, social, and economic challenges.
Environmentally, silicon production is energy-intensive, particularly during the reduction of silica to metallurgical-grade silicon in electric arc furnaces. This process emits substantial carbon dioxide, undermining its green potential. Additionally, mining for quartz can lead to habitat destruction, water pollution, and increased carbon footprint due to the reliance on fossil fuels for energy.
Socially, the silicon supply chain raises concerns about labour conditions, particularly in major producing countries like China. Reports of poor working conditions, low wages, and inadequate safety measures highlight the need for improved labour practices and stronger enforcement of regulations. Furthermore, the displacement of communities due to mining activities can lead to social unrest and loss of livelihoods, exacerbating inequalities.
Economically, the silicon industry is subject to market volatility, driven by fluctuations in demand for electronics, solar panels, and batteries. Dependence on a few key countries for silicon production and product manufacturing also poses risks to global supply chain stability. Trade restrictions, geopolitical tensions, and policy changes in these regions can disrupt the supply and lead to price spikes, impacting downstream industries and global efforts to scale up renewable energy technologies.
Addressing these challenges requires a multifaceted approach, including advances in sustainable mining practices, improved labour standards, diversification of the supply chain, and investment in recycling technologies to reduce the environmental impact and ensure a stable, ethical supply of silicon.
Sustainable silicon pathways
Reducing the environmental impact of the silicon supply chain and downstream manufacturing can be achieved through several strategies guided by invaluable life cycle assessment (LCA) insights, such as those provided by Minviro, and highlighted by the IEA (IEA, 2022).
LCA quantifies the environmental impacts associated with a product, process or system, and the manufacturing of decarbonisation technology is a perfect example of a complex, multifaceted supply chain that can benefit immensely from the granular detail provided by the approach. This includes the direct and, importantly, embodied impacts related to all materials and energy consumed in the entire process, plus any environmental emissions, to give a comprehensive overview of sustainability performance. This can reveal ‘hotspots’ - inputs or areas in the supply chain with particularly high impact potential (either due to material/energy demand or the embodied impact of creating these inputs further up the supply chain), and present key targets for impact reduction efforts. Examples of optimising silicon products for environmental performance based on LCA insights include:
- Shifting to renewable energy sources for powering silicon production facilities can reduce the carbon footprint. Solar, wind, and hydroelectric power can replace fossil fuels used in the silicon supply chain.
- Improving energy efficiency in process steps by introducing energy-saving technologies in silicon purification and crystal growth processes, reducing the overall project energy demand.
- Increasing circular flows within the supply chain, including recycling of silicon materials from end-of-life products, such as solar panels and electronic devices; this has the double effect of potentially reducing impacts, and generating secondary supply streams to reduce strain on primary production.
- Adopting sustainable mining practices in silica extraction, such as minimising land disturbance, reducing water usage, and ensuring proper waste management, all of which would lower the material consumption per product.
- Implementing advanced emissions control technologies can reduce pollutants released during silicon processing, including capturing and reusing byproducts in the process stream, and improving filtration systems to prevent air and water pollution.
- Developing innovative, more efficient silicon-based technologies that can perform at competitive levels but with reduced material consumption.
By integrating these strategies, the silicon supply chain can become more sustainable, minimising its ecological footprint throughout the life cycle from raw material extraction to end-of-life disposal. Please contact Minviro for more information, or to kick start your sustainable silicon journey.
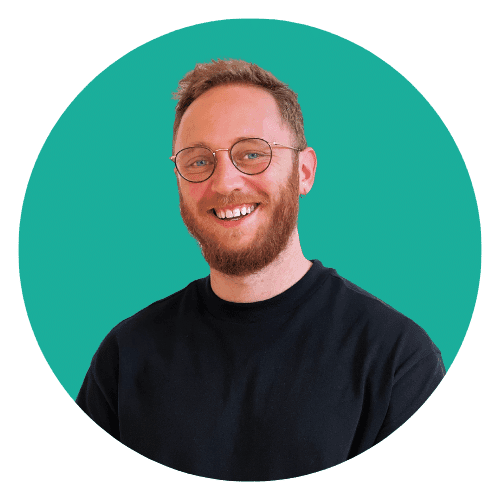
Jordan Lindsay
Jordan completed his PhD in Geochemistry at Camborne School of Mines and is the head of Minviro's Research & Development team.
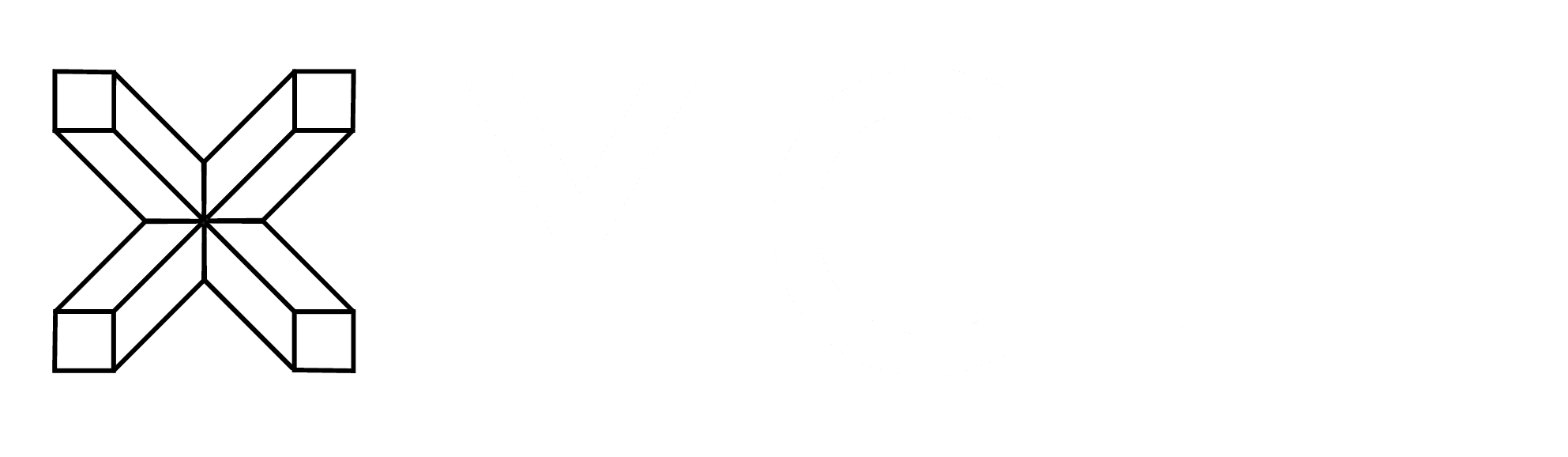